Hey Kyle,
What I meant is approximately 8 mm. You could also use 1/4″ (6.35 mm) or 3/8″ (9.525 mm). What I meant is that for milling pockets, I would consider a 1.125″ (29 mm) bit as much too large.
Here are some links where to buy milling bits:
Milling bits in Imperial/U.S. Customary units are uncommon in Europe, and at least as far as I know, elsewhere too (except USA and Canada).
Goran tek-en, CC BY-SA 4.0, via Wikimedia Commons
Here in Europe we commonly use bits with 6, 8, 10 or 12 mm shanks on ER collets (that I buy from spindle manufacturer), and the Makita hand trim router is sold outside U.S. with 6 and 8 mm collet:
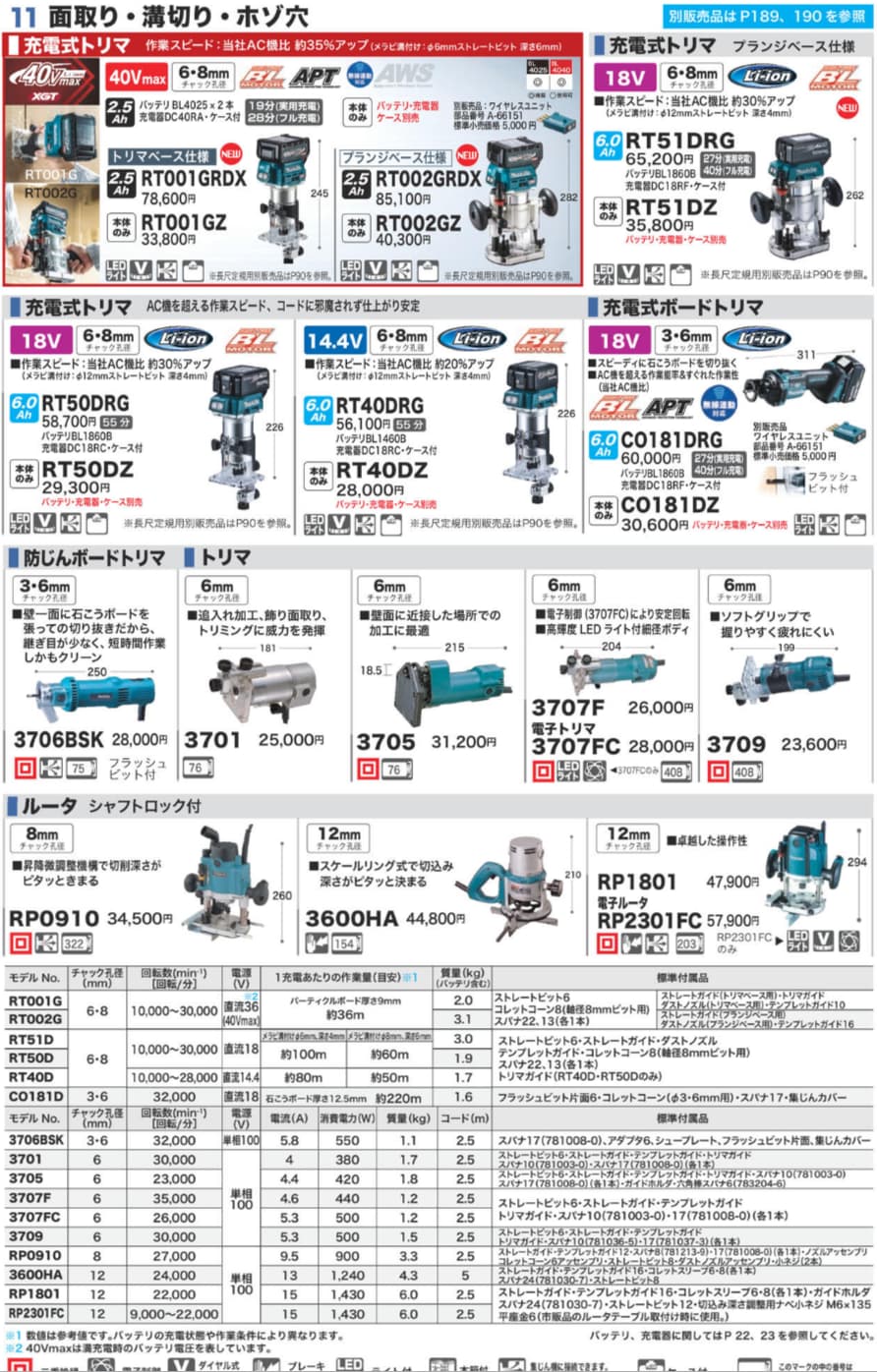
www.makita.co.jp: Routers – Catalog page
[
)
www.makita.de: RT0700C (discontinued)
www.makita.de: RT0702C (current model)
You are used to use metric units in South Africa I assume? Maybe because you have imperial history and also many goods are imported from the U.S., you use imperial units too?

We mainly sell to U.S. rather than to buy there:

Of course here inch collets are also available (for both trim router (UK version) and ER spindles) for those who want to use milling bits from the USA, but it’s not that common.
I think you can achieve surfacing the wasteboard with such a large bit in the hand trim router, and sure, many do, but surfacing the wasteboard means removal of only shallow depth. I would not use such a bit for milling pockets, especially not with high plunge rate. I would use an end mill (which is good for plunging) and a high speed.
Also keep in mind that the hand router has only approx 0.75 kW power (which due to poorer efficiency of universal motor in comparison to spindle induction motor only corresponds to 0.5 kW spindle) and a 1.125″ (29 mm) surfacing bit is a very large diameter. Usually in normal use of a hand trim router you don’t use bits larger than 1/2″ (12.7 mm). It’s simply too much couterforce with such a large diameter bit for the weak motor, at least when you try to do deep pockets.
Also what I meant is that the trim router is not made for longer and/or stationary use. I did not buy one for use in the Onefinity.